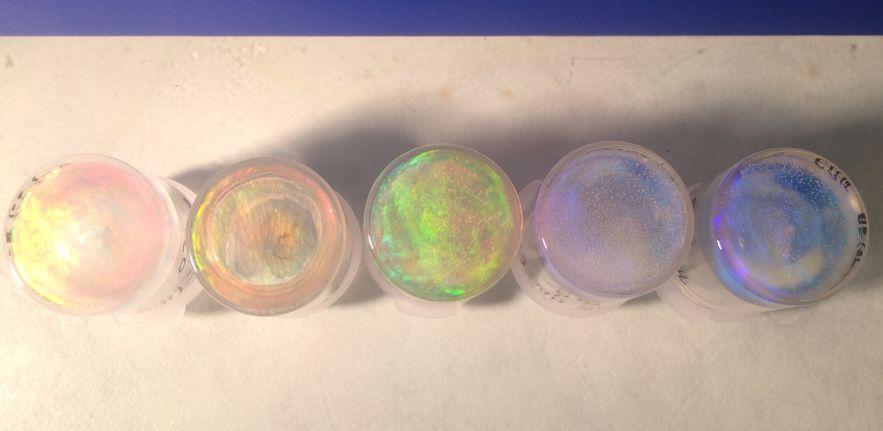
The Cambridge MRes students are offered a number of long project options from supervisors who are willing to support these projects. The projects start in April and complete in August, with the assessment consisting of a mid-term presentation, end of project presentation and assignment. The projects are spread across the ultra precision community within the UK, with some time spent at the supervisor’s location, and the remainder at Cambridge.
Here are short abstracts of the long projects conducted in 2017:
Colouring of coinage alloys and generation of reflective holograms through direct laser writing, Pete Atkin
The Royal Mint is interested in modernising and improving the manufacturing process and design of their circulation and special addition coins. Of particular interest is the use of laser induced oxidation to rapidly colour coins. The first aim of this project is to assess the applicability of laser induced oxidation for a range of coin alloys, as well as assessing the durability of oxide layer for everyday use. A further aim of the project is to assess the use of ultrafast lasers in the production of reflective holograms on the coin die, which can be successfully transferred onto coins during the minting process. If successful this could be used as an added security feature in future generations of coins.
Experiments to characterise an insitu TEM liquid cell, Elkin Lopez-Fontal
Self-assembled systems play a crucial role in Nature. Learning the rules of self-assembly is directly related to evolution and how living and non-living systems operate. Furthermore, it has been extensively shown that the intrinsic characteristics of self-assembled systems can be exploited at the technological level. Having highly ordered molecular assemblies is attractive as they present unique properties that could be used for making functional materials from nanoscale components. Here, we are interested in solution-phase self-assembly of nanocrystals using aqueous electrolyte solutions, where crystal nucleation can be observed and imaged in real time by using a liquid cell electron microscopy (LCEM).
Precision Finishing of an Additive Manufactured Component, Jack Cook
Powder bed fusion additive manufacturing techniques enable the redesign of complex assemblies into single parts. It is therefore a useful fabrication process within the aerospace industry where it can be used to reduce the lead time, mass and cost of a component. However the raw additive manufactured component will have form deviation due to trapped thermal stresses, a large surface roughness relative to the powder size and porosity defects. The purpose of this project is to define the post processing techniques required to manufacture and validate new generation of additive manufactured optics.
Production Process Monitoring using Holographic Techniques, Peter Christopher
Peter is modifying an ultra-fast camera previously developed within the Centre for Industrial Photonics so that it will fit within an industrial processing chamber; manufacturing inkjet nozzles via percussion laser drilling. The primary goal of the project is to understand the subtle light, matter, plasma dynamics and the effect they have on nozzle quality. Data generated within the project should look to provide the sponsor with potential limitations of the process (e.g. maximum laser frequency) and a potential route for future optimisation of the process as lasers are replaced.
Smart Cellulose Photonic Fibres, Charlie Barty-King
Plant-based polysaccharides, such as cellulose and its derivatives, are receiving increasing interest for a diverse range of applications as an environmentally friendly, biocompatible and potentially-edible alternative to conventional plastics. One such example is hydroxypropyl cellulose (HPC), which is known to form a chiral nematic liquid-crystalline phase in water that displays vivid, iridescent colour without the need for any dyes or pigments. Within the bio-inspired photonics group (BIP) of Silvia Vignolini at the Department of Chemistry, Charlie Barty-King is investigating the self-assembly and processability of new HPC formulations to better understand their potential use as a cheap and easy to prepare photonic material. This project will initially focus on understanding how to achieve fine-control over the colour of the HPC mesophase, before exploring how to translate this colour to the solid-state, via a range of chemistries. Compatibility of these HPC-based materials with industrial processing techniques will be a strong consideration throughout, with the intention to focus towards roll-to-roll film deposition and fibre extrusion methodologies.
Synthesis of three-dimensional nanostructures incorporating advanced magnetic materials, Fanfan Meng
The digital revolution lived during the last decades has been possible thanks to the continuous miniaturization of integrated circuits and storage devices. However, the need of lower power consumption devices with added functionalities, makes necessary the development of new types of lithography techniques[1]. The Thin Film Magnetism Group in Cambridge is investigating new ways to process and store digital information exploiting novel effects in magnetic nanostructures [2,3]. In this project, we will investigate the fabrication of 3D nanostructures incorporating advanced magnetic materials for applications in spintronics. A new multi-step manufacturing process, involving 3D nano-printing methods and thin film deposition processes will be developed.
[1] Waldrop et al, Nature 530, 145 (2016).
[2] Lavrijsen et al, Nature 493, 647 (2013).
Wide area laser manufacturing of self-cleaning surfaces, James Macdonald
Laser texturing of stainless steel surfaces to make them hydrophobic is a surface modification technique rapidly approaching industrial adoption and practical value. The process involves the creation of laser induced micro and nano structures which modify the wetting behaviour of water in contact with the surface. This project has been designed to answer a number of research questions. Firstly, this project will present the state of the art regarding the contribution of surface morphology and chemistry to the mechanism of hydrophobicity. Secondly, a laser fabrication technique will be explored, focused on delivering superhydrophobicity for food processing equipment. Thirdly, the durability of the fabricated surface will be optimised and finally the process will be scaled to wide area manufacturing.