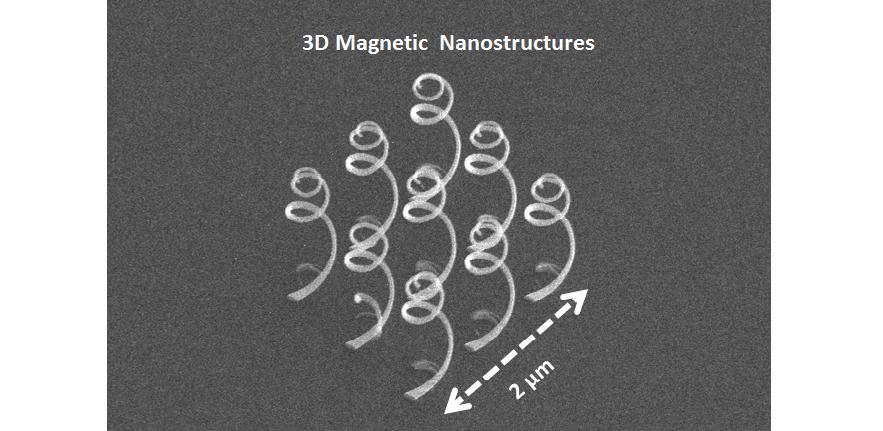
The students are offered a number of mini project options from supervisors who are willing to support these projects. The projects start in January and complete in March, with the assessment consisting of a mid-term presentation, end of project presentation and poster, and assignment. The projects are spread across the ultra precision community within the UK, with some time spent at the supervisor’s location, and the remainder at Cambridge.
Here are example short abstracts of the mini projects:
3D laser biological imaging system, Pete Atkin
High resolution 3D tomographic imagining of biological systems is a growing area of research. Laser ablation tomography is of particular interest in this field due to its ability to remove material layers for high resolution imaging at a relatively high rate in comparison with rival technologies. However, current laser ablation tomography systems often suffer from issues with ablated surface quality. The purpose of this project is to assess the use of ultrafast laser ablation to achieve high surface quality whilst maintaining high material removal rates and resolution. If successful this project should provide the ground work for the design and manufacture a fully integrated high-precision laser ablation tomography system.
Precision motion via additive manufacturing, Charlie Barty-King
Professor Richard Leach, based out of Nottingham University, leads one of our CDT in UP groups, with a particular focus on ‘Information-Rich Metrology’ in developing new methods of measurement in areas of interest such as advanced manufacturing. Charlie Barty-King is involved in the design of an additively-manufactured precision flexure stage with relatively high working range yet also having high repeatability. This fits into a larger project that aims to create a self-calibrating micro-CMM. The end-goal of Charlie’s work is to suggest some flexure designs and back-up the design choices with simulation data, and if time, experimental data.
Laser writing system for micro patterning roll-to-roll substrates, Peter Christopher
Flexible electronics have been possible in the laboratory for several decades but have only just started to make the transition to consumer products. Peter Christopher is part of a partnership between Heriot-Watt University and the CDT-UP, looking to adapt one such process into an industrially relevant technique. By building a prototype roll-to-roll machine that patterns silver nanoparticles using laser light and a deformable micromirror array, Peter aims to help bridge the gap between the laboratory and the marketplace.
A MEMS device for the measurement of micro- and nano- mass, force and flow, Jack Cook
Current traceable measurements of mass and force require a calibration chain to the International Prototype of the kilogram (IPK) held at the Bureau International des Poids et Measures (BIPM) on the outskirts of Paris. Consequently calibration for measurements of micro- or nano- forces and masses require several scaling steps which increase the relative uncertainty on the measurement. The redefinition of the kilogram will enable Kibble balance techniques to measure mechanical force with direct traceability to the SI through electrical measurements. The project involves a feasibility study and basic design analysis on a micro device for traceable measurements of micro- and nano- force and mass.
Optimised particle morphology in Supersonic Laser Deposition, Georgios Kokkinos
Metallic coatings offer multiple functionalities to mechanical components. In the past, coating processes, such as laser cladding and cold spraying, involved melting of material causing embrittlement or involved expensive carrier gases such as helium. The supersonic laser deposition has been developed at the University of Cambridge and has attracted the interest of the industry because it has been proven to create high quality coatings without involving the aforementioned drawbacks. In this process, powder particles contained in Nitrogen are accelerated to supersonic velocities to impact a substrate which is soften by a laser beam. Upon impact, plastic deformation of the substrate and particles is responsible for bonding. An important process parameter is the size of the particle. It is expected to be one of the decisive factors in determining the quality of the coating. This work is about experimentally determining the effect of different particle diameters on the coating by experimenting with stainless steel and stellite 6® powders. The outcome of this research will offer greater understanding on the process and pave the way for new research areas and improvements.
Measuring the Resistance of CNT Fibres, Jamie Lake
In-line and real-time characterisation methods are of huge importance to the reliable and reproducible synthesis of carbon nanotube fibres. At the University of Cambridge, the MML currently synthesise some of the most conductive and strongest fibres producible. The synthesis of such fibres is simple in theory; following a technique pioneered by Professor Alan Windle, the Cambridge Process. However, precise control of the many complicated variables at play requires an advanced control system. Small changes in these variables can be detrimental to the quality and uniformity of the fibre. Therefore, the more information a control system has, the stronger its feedback mechanism. Measuring the resistance of the fibre as it is wound from the reactor could allude to changes in its fundamental properties, breaks in the fibre or provide a signal proportional to another quantity i.e. iron content. Using a non-contact RF eddy-current sensing prototype device, a proof of concept analysis is underway to determine how a device of this sort can be best employed to provide useful feedback information.
Ultra-precision control by condensation and self-organisation, Elkin Lopez-Fontal
Deposited aqueous drops on a hydrophobic surface can be driven to self-organise and pack together to make ordered arrays. Those arrays can, in turn, be captured in a polymer matrix to make unique microstructures. There is a wide range of possible applications, such as cell scaffolds, optical telecommunications, sensors, drug delivery coatings and filters. The idea to be able to modify the size of deposited drops can increase their applicability. We at the Fluids in advanced manufacturing group are at the moment investigating that possibility.
Advanced fabrication of three-dimensional magnetic nanostructures using Focused Ion Beam, James Macdonald
3D Data storage and logic devices are a current focus of research. This is driven by the historical and future growth in computer storage capacity and the approaching fundamental limits of miniaturization. The benefits of proposed 3D data storage approaches involve higher information density and novel functionalities. A significant challenge for the realization of these techniques is in the physical fabrication of the complex structures required. This project focuses on the technique of focused electron beam induced deposition to create arrays of 3D magnetic nanostructures. In essence, this project aims to accomplish 3D printing of magnetic material at the nanoscale.
Verification of PFPE as an imprint mould for R2R Scalable Fabrication, Tanya Mangoma
Scalable fabrication imprint techniques used in the production of large area patterned materials (e.g. electronics and surface texturing) have been hindered by lack of durable template moulds that can replicate structures with high fidelity. Traditionally, Polydimethylsiloxane (PDMS) moulds have been used. However, due to low modulus and poor chemical resistivity, PDMS moulds have thus far produced non- replicable imprint structures with relatively low throughput than that desired. As a result, alternative mould materials, together with novel fabrication techniques, are being sort after. In recent times, Perfluoropolyether (PFPE) has gained interest as a possible material for mould manufacture. This project focuses on verifying PFPE as a potential mould material. The first half of the project focuses on developing a method to create PFPE imprinting moulds using equipment currently available within the Institute of Manufacturing. This includes optimisation of both the chemistry of the material and the physical preparation steps of the mould. In the second part of the project,a comparison of the replication fidelity and durability of the manufactured PFPE moulds to that of conventional PDMS moulds is done. To achieve this, PFPE and PDMS moulds are used to R2R imprint micron to sub microns structures on photoresist coated PET film. The features are then analysed using optical and SEM imaging techniques to validate both fidelity and durability. The results of this project aim to verify the potential of PFPE moulds for large scale imprinting and to bring a better understanding of the limitations of the currently equipment being used for the fabrication of the PFPE mould.
Design and fabrication of a Transfer Printing Apparatus for Carbon Nanotubes Structures, Fanfan Meng
Advanced carbon nanotube structures are used in many applications ranging from bullet proof fabrics to battery electrodes. For certain applications, including micro sensors and energy storage devices, carbon nanotubes are required to be transferred from the silicon substrate on which they are synthesised, to an appropriate substrate for the targeted application. This project aims to develop a dedicated transfer printing apparatus so that CNTs can be transferred in a scalable and reproducible way.
Tuning chemistry through controlled micro-nozzle flow, Tommy Zhao
Covalent bonds of macromolecules can break in strong elongational flow fields. This phenomenon is of importance in both industrial and research environments when done in a controllable fashion, such as the use and degradation over time of drag-reducing polymers for oil recovery and fluid conveying and the mechanical fragmentation of DNA for high throughput gene sequencing. The Fluids in Advanced Manufacturing group in Cambridge has developed a multi-scale model to understand the macromolecules scission and degradation through complex fluid streams. The current project aims to build an experiment to validate, calibrate and improve the model, particularly focusing on micro-nozzle flow. If successful, the refined model will be among the first ever works in this area.